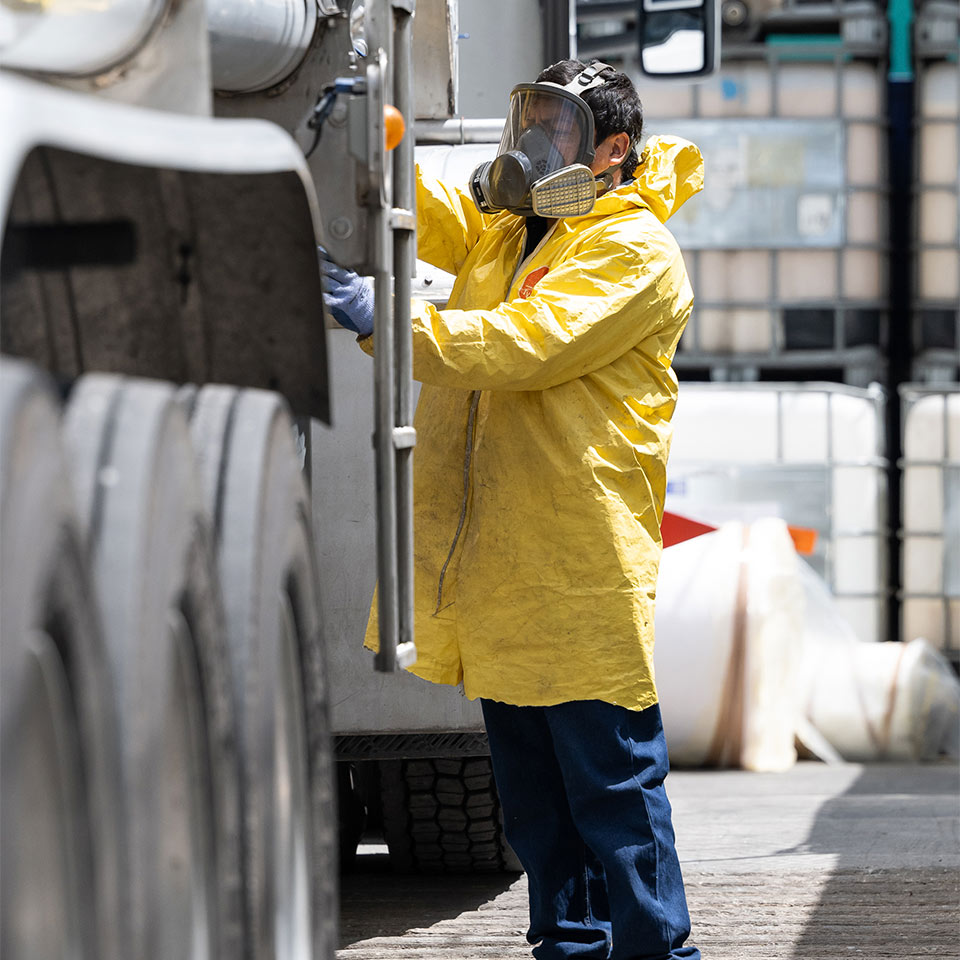
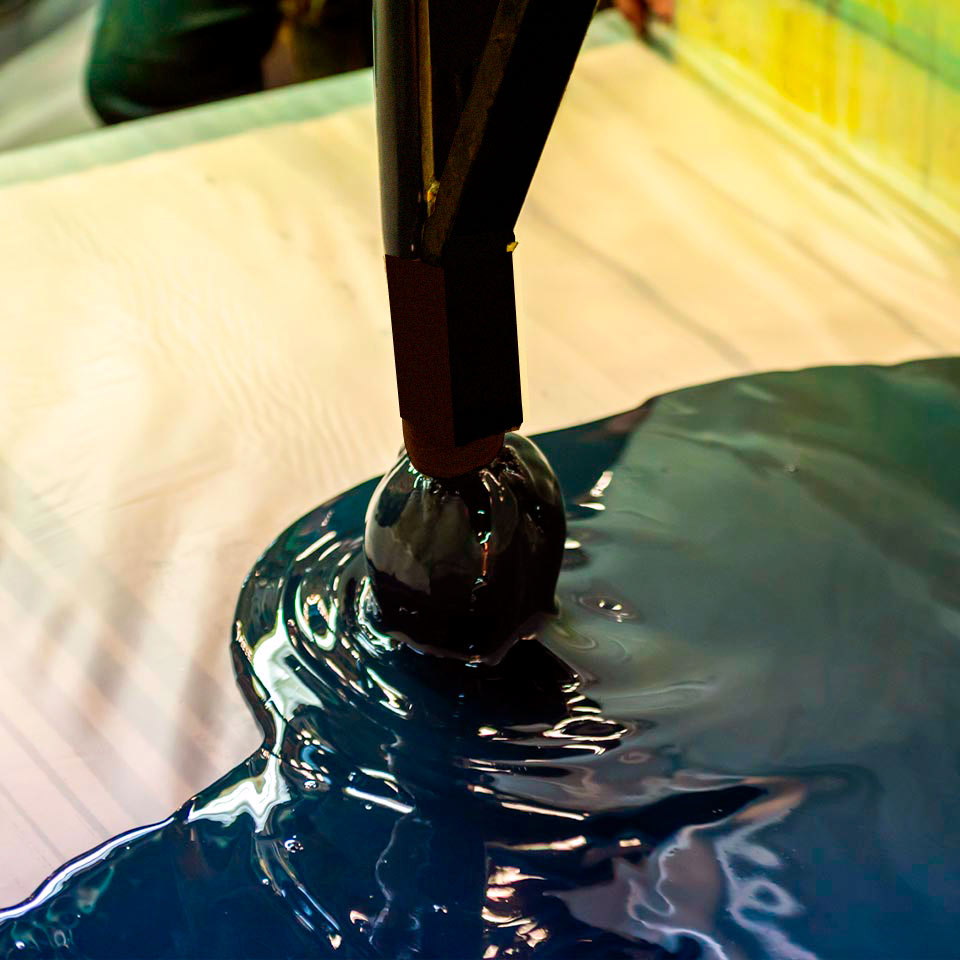
FOAMING
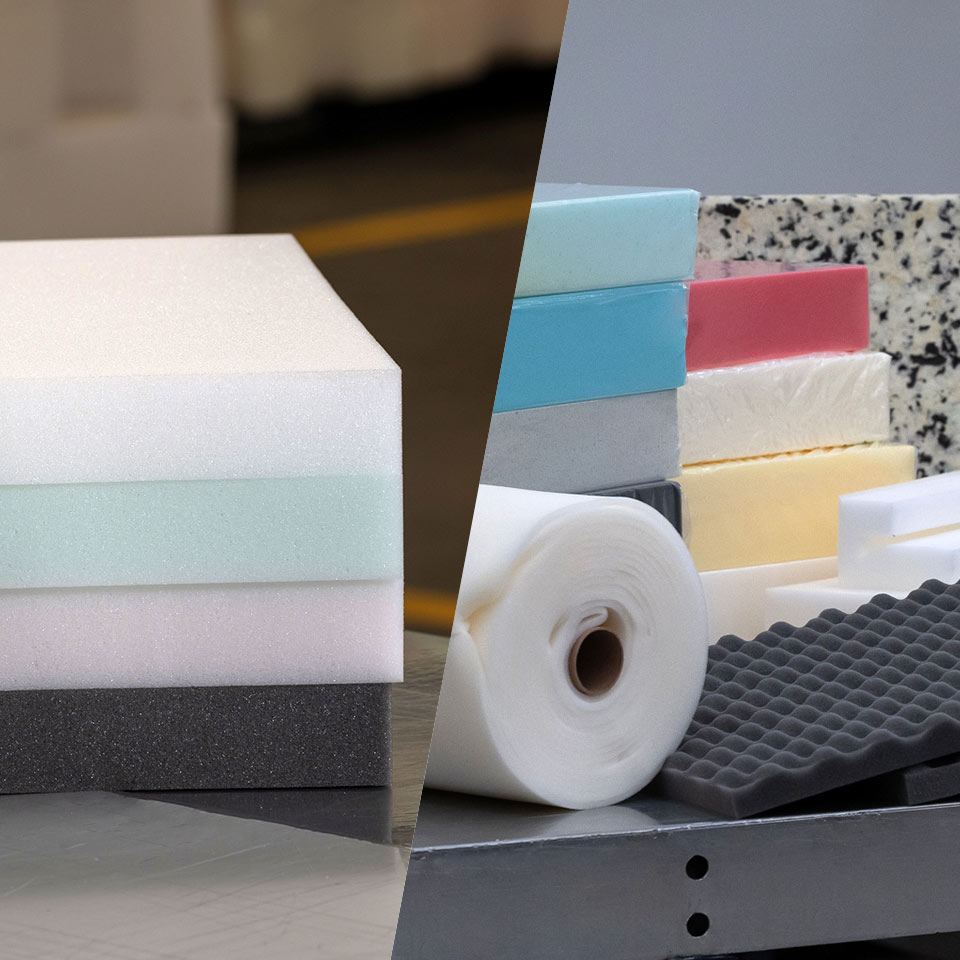
DIMENSIONED, LAMINATED
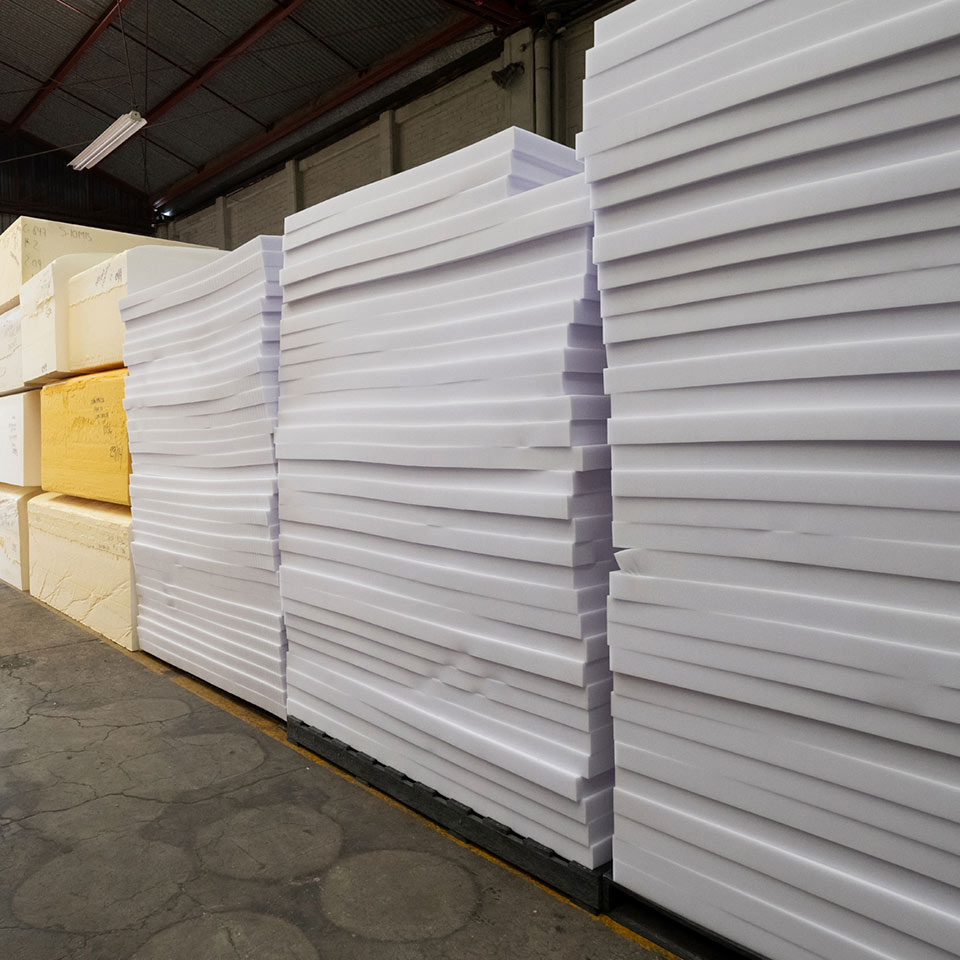
LAMINATE
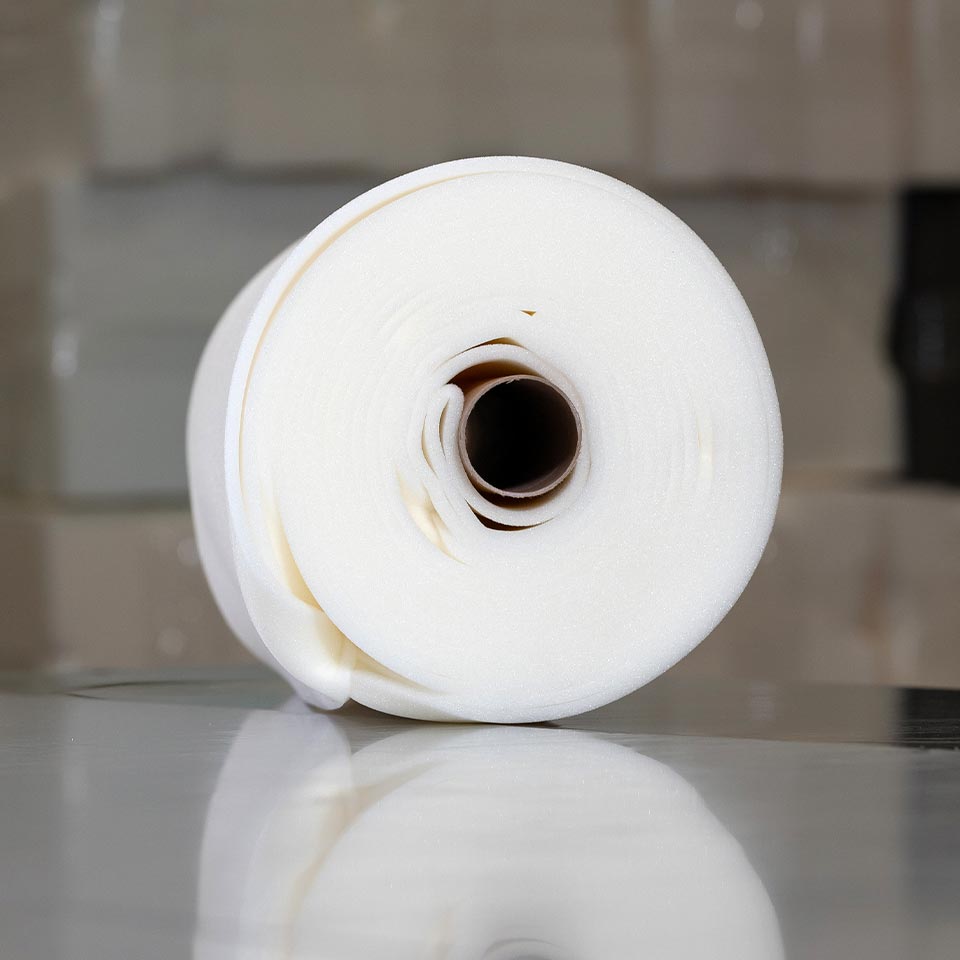
PEELER
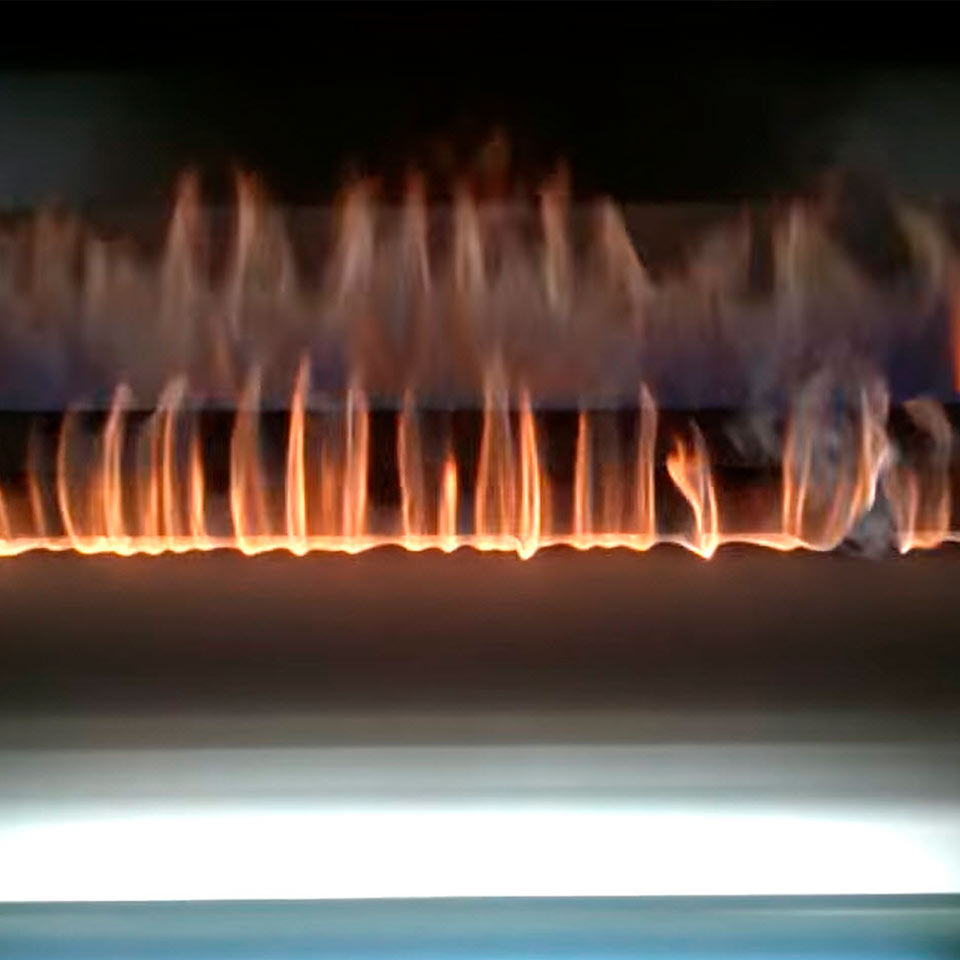
BONDEADO IN THE FLAME
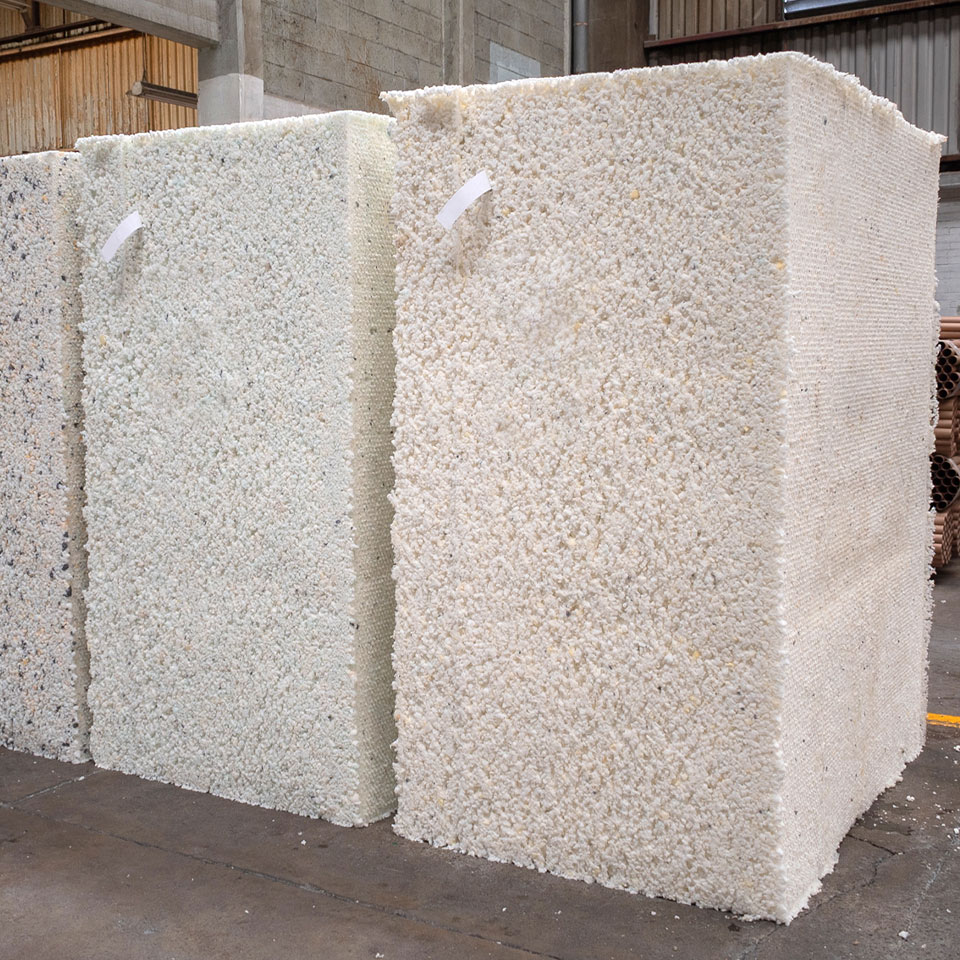
Polyol and TDI (toluene disisocyanate) are mixed with other components and poured as a liquid into the "pour plate" of the skimmer in a continuous manufacturing process.
The liquid is poured into the machine, forming foam blocks that are created from the reaction of the substances. The foam must be allowed to cure to complete the polymerization.
Computerized machines in which they design and develop special, vertical, horizontal and curdling cuts. All this according to customer specifications.
The foam is processed with a carousel cutter to obtain sheets with a minimum thickness of 2 mm horizontally.
For this product the Looper and Peeler machines are used; Its main applications are in the automotive sector, clothing, mattress, among others, which require thicknesses from 2 mm and lengths up to 300 meters. The sale of this product is in roll.
Process that involves the adhesion of foam with different fabrics and vinyl. Process performed with flame. It is used in the automotive, footwear and intimate apparel market.
Foam derived from the trimming of the aforementioned processes, becomes drageing and is processed forming the binder. In its process, polyol and TDI are mixed, poured into block molds. The use in the market is the mattress and under carpet, among others.